What preparations should be done before the
injection mold factory debugging
What preparations should be done before the injection mold debugging
Rigorous attitude is the premise of successful work, injection mold debugging must be prepared before all work.
The injection mold debugging must be issued by the external cooperation department or the production department to start the preparation. The first step is to check the drawings, in which there are two drawings, one is the drawing of the mold debugging product, and the other is the drawing of the mold. Understand the material, geometry, function, and appearance requirements of the product according to the product drawings, such as color, spots, impurities, scars, depressions, etc. Injection Mold Manufacturing
Equipment inspection
Check the technical parameters of the equipment: the diameter of the positioning ring, the nozzle sphere size R, the nozzle diameter, the smaller mold thickness, the larger mold thickness, the larger mold thickness, the larger mold thickness, the larger mold thickness, and the larger mold thickness Die stroke, rod spacing, top method meet the requirements of the Ministry of testing, ready to work before driving.
The test equipment should be identical to the machine at the time of production. This is because the technical parameters of the equipment are related to the technical standards of the test product. Temperature fluctuations, pressure changes, empty cycle times and the stability of mechanical and hydraulic transmissions will affect the quality of the product.
Material preparation
Check the specifications, models, grades, additives, masterbatches, etc. of the processed plastic raw materials to meet the humidity requirements of the raw materials, and dry to determine the proportion.
In principle, the raw materials should be according to the regulations of the raw materials, because the mold is designed based on the physical properties of the raw materials. Injection Mold Design Supplier
Mold inspection
Before the mold is installed on the injection molding machine, the mold inspection on the mold drawing should be carried out to detect the problem in time and carry out the maintenance mode. According to the assembly drawing of the injection mold, the size of the mold, the size of the positioning ring, the size of the inlet of the main channel, the size R of the sphere, the inlet and outlet of the cooling water, the height and width of the pressure plate can be checked.
Cooling water pipes or heating wires
Open the mold cooling water pipe or heating wire to check, if using hydraulic or motor surface, it should also be connected to check.
Tools & Accessories
Test kits are special tools for testers, garments in a portable toolbox for easy portability. Each commissioner should have one set. Die-related tools are manipulators, pads, checking die thermometers, checking the dimensions of die card equipment, checking tools used, and operations of commonly used copper bars, copper and sandpaper spare parts.
Daily Plastic Two-Color Cup Mould
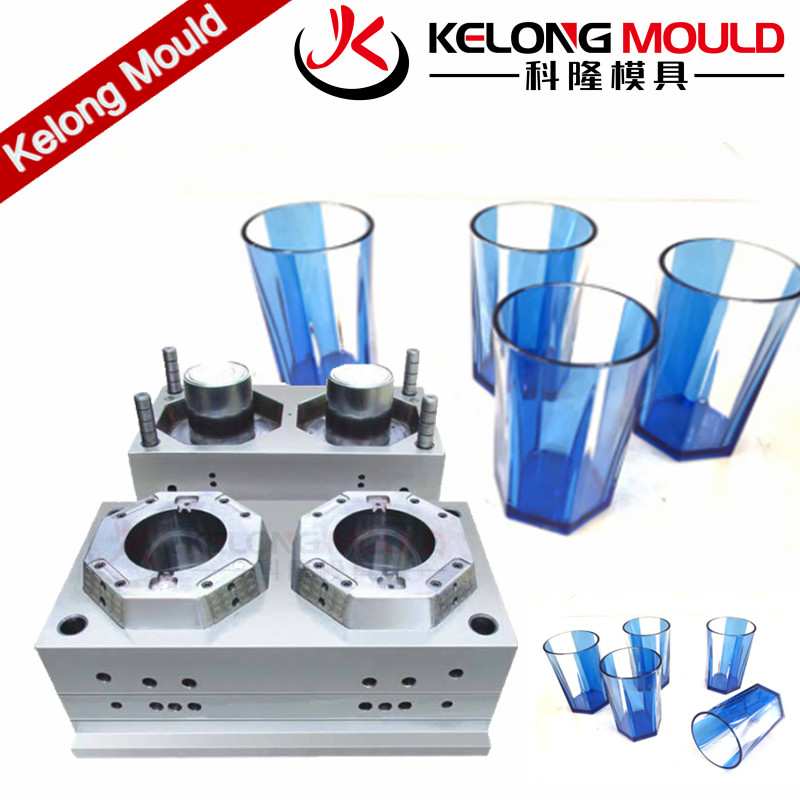
Plastic cup mould cooling: Using circulating water to effectively improve product quality and mould ejection efficiency. Mid-term treatment of plastic cup mould: Quenching and tempering to improve hardness. Post-processing of plastic cup mould: Post-processing: nitriding treatment, the surface hardness of plastic mould is greater than HV850, quenching treatment, the overall hardness of the mould cavity can reach more than HRC48 degrees.