PP Plastic Table And Chair Mould
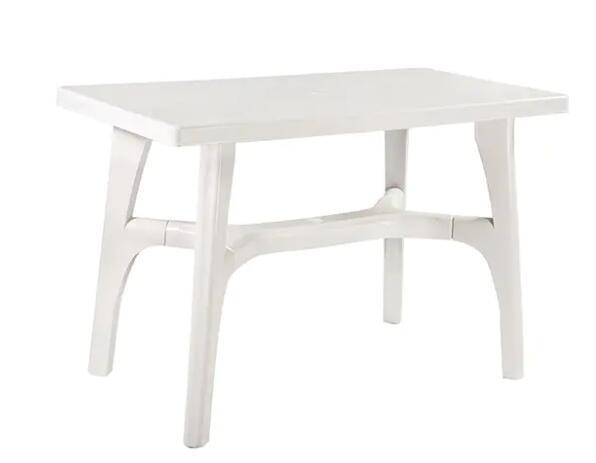
Facebook Twitter LinkedIn Youtube
The modern household is filled with appliances and electronic devices designed to make daily tasks more convenient and efficient. Behind the production of these products lies a crucial manufacturing c...
In today’s fast-paced manufacturing industry, technological advancements are reshaping the way products are developed and produced. One area where this progress is particularly visible is in the field...
In the constantly evolving world of household product manufacturing, the importance of precision, efficiency, and durability cannot be overstated. Among the essential tools contributing to these quali...
The global demand for high-quality household appliances has driven continuous advancements in manufacturing processes and mould production technologies. However, despite steady improvements, producing...
The automotive industry is continuously evolving, and bumper production is no exception. The role of automotive moulds in bumper manufacturing has become increasingly important as design complexity an...
Choosing the right automotive mould for bumper production is a critical decision that can significantly impact both the quality of the final product and the efficiency of the manufacturing process. Ch...