The structure of the injection
molding machine mainly includes a clamping device, an injection device, an electrical control system and a hydraulic transmission system. The function of the mold clamping device is to realize the opening and closing of the mold, to ensure the reliable closing of the molding mold during injection, and to eject the product; the mold clamping device mainly consists of front and rear fixed templates, moving templates, tie rods for connecting the front and rear templates, mold adjusting devices, It is composed of mold clamping cylinder, connecting rod mechanism and product ejection device. The injection device mainly plasticizes the plastic uniformly, and injects a certain amount of molten material into the cavity of the mold with sufficient pressure and speed. The injection device is mainly composed of plasticizing parts (screw, barrel and nozzle), as well as hopper, metering device, transmission device, injection and moving cylinder, etc. The hydraulic and electrical control system is to ensure the accurate and orderly work of the injection machine according to the predetermined requirements and actions of the process. The hydraulic system and the electrical system are organically organized to provide power and control the injection machine.
Plastic molds are generally composed of mold cores, mold bases, auxiliary settings, auxiliary systems, auxiliary parts, and dead angle treatment. The mold core is the core part of the plastic mold, and it is the most important part in the mold. The forming part of the plastic product is in the mold core, and most of the processing time is also spent on the mold core. However, some simple molds have no mold core part, and the product is formed directly on the template. The mold base is the most basic frame part of the plastic mold. It is generally ordered directly from the standard mold base manufacturer to save design time, so it is called the plastic mold standard mold base. Auxiliary settings are provided with ring holes, KO holes (top stick holes) and so on. The auxiliary systems of plastic molds are: pouring system, ejection system, cooling system and exhaust system. Sometimes the plastic materials used need to be heated at a high temperature, and some molds also have a heating system. Common auxiliary parts include positioning ring, sprue bushing, thimble, grab pin, support column, ejector plate guide column guide sleeve, garbage nail, etc. Some of them are standard parts and can be ordered together directly when ordering the mold base. Part of it needs to be designed by yourself. Dead angle treatment structures such as sliders, inclined roofs, hydraulic cylinders, etc. In fact, the plastic mold is not difficult, no matter how the plastic product changes, for the plastic product mold, its structure is the above-mentioned aspects. The difference between the molds is the size of the mold. Auxiliary parts, auxiliary settings, auxiliary systems are located or in different ways. The method, structure, size, etc. of dealing with dead space have changed. Of course, to make the designed mold easy to process, easy to assemble, long in service life, moderate in price, and good in formed products, design experience is particularly important.
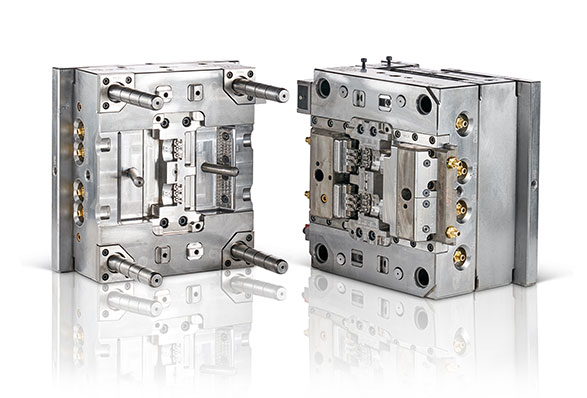