PP Plastic is used in a wide range of applications from medical supplies and pharmaceutical products to automotive parts, such as dashboards, instrument panels, door trims and more. It is resistant to strong chemicals and steam sterilization, making it a popular material for these types of products.
Injection molding is a very common way of manufacturing PP Plastics. This process involves a machine which melts resin pellets and then injects them into the mold cavity via a runner system to form a finished part. This method is a very cost-effective process for large production runs but it can also be expensive if you're producing small batches of PP or other injection molded parts.
Shrinkage is a common problem with injection molded parts, especially if the plastic has been exposed to heat. This is because the density of the injected polymer changes during cooling, causing a volume contraction of the plastic part.
There are some ways to minimize shrinkage during the cooling phase of the injection process. One way is to make sure that the part is properly cooled before it's removed from the mold. Another is to provide a protective cover over the plastic, such as a plastic sheet or vapor barrier.
Some other techniques to reduce shrinkage include minimizing the number of parts in the mold, using a tighter grip on the part during injection and avoiding using high-shrink materials such as acetal and nylon.
PP Plastic in the Food Industry:
PP plastic is often used in the food industry to produce containers such as cups and bowls. The material is durable and can stand up to a variety of temperature conditions.
It can also be used for packaging, such as flexible and rigid packaging. In addition to this, PP plastic is commonly used in the healthcare industry to produce petri-dishes, syringes, specimen bottles, pans, and pill dispensers.
The use of a polymer for a tabletop is a very creative and innovative idea that can result in a very functional, lightweight, and durable product. The invention uses a foam core encapsulated within a polymer shell to create a plastic table that is both light and strong.
This method of forming a rotationally-molded tabletop is able to produce a solid and durable plastic table with multiple layers of a single polymer material which can be fabricated in one pass. It allows for a greater material placement into the weakest areas of the mold, and it produces a table top that keeps its shape and resists delamination because both the foam core and the polymer skin are of the same species and can integrally bond while at elevated temperatures.
20L Sorting Trash Can Mould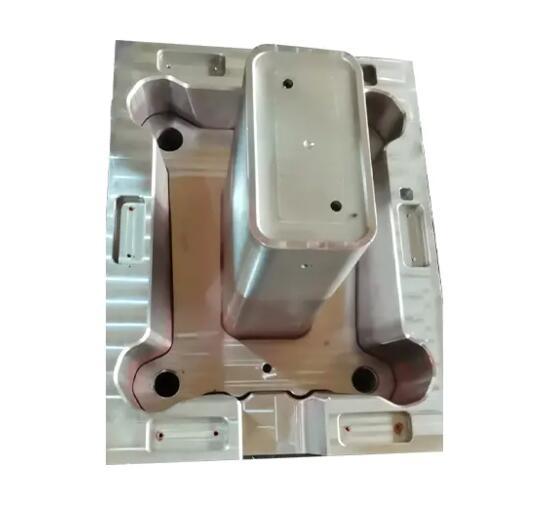
The classification trash can mould made by Kelong is composed of moulds such as the lid, handle, bucket, foot pedal, etc. The ejection of the mould adopts the structure of pushing plate + air top, and the production efficiency of the product can be increased by more than 50% (above 3,000 pieces can be produced in one day). The mould body is made of imported p20, 718 high-quality mould steel or imported alloy steel. The hardness of the steel is hrc28~hrc38, and the mould is tempered and nitrided. The classification trash can mould has good comprehensive mechanical properties, high rigidity and small deformation. With internal and external chrome plating, mirror polishing, it has good flatness, high precision, easy demoulding, high surface hardness (greater than hv850), wear-resistance and no deformation, which greatly enhances the life of the mould (at least 500,000 moulds).